Safety by Design
Adopting a safety mindset begins at the top, as companies recognize the need to integrate safety into a culture of respect and accountability. Safety is a critical concept – not only because we all want to return to home safely each day, but because projects that complete with zero recordable safety incidents are not only well-managed, but a direct reflection of the company’s commitment to safe work practices. Making safety a focus in the design and construction of upgrades and new facilities is more than checking a box. When properly implemented, safe work practices eliminate an array of potential issues and help reduce costs.
Safety by Design is a mindset. It starts when, as an architect, you realize that your license is an obligation to protect the health and safety of the public. That applies both during construction and when the final design is open to its intended use. It is a prerequisite for good design.
– Thom Shelton, Gensler Dallas
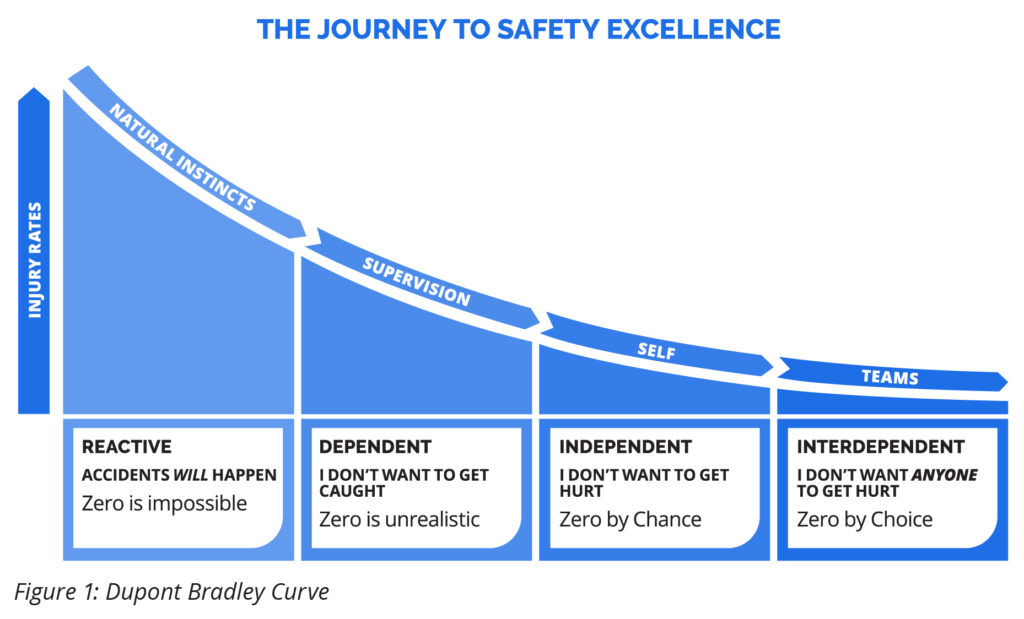
In the built environment, the highest safety risks are on the construction site, so this responsibility traditionally lands on the shoulders of the constructor. As architects move along the safety culture curve toward being interdependent (Figure 1), all design professionals should look for opportunities to provide designs that are safe to build, occupy and maintain. Known as Safety by Design (SbD), this approach incorporated continuous improvement principles at both the macro and project levels.
As demonstrated in Figure 2, the general activities that should be incorporated into each project include:
- Establishing project-specific SbD requirements.
- Executing ongoing SbD implementation practices.
- Executing project-specific SbD workshops and reviews.
- Soliciting and incorporating opportunities for improvement at the project and program levels.
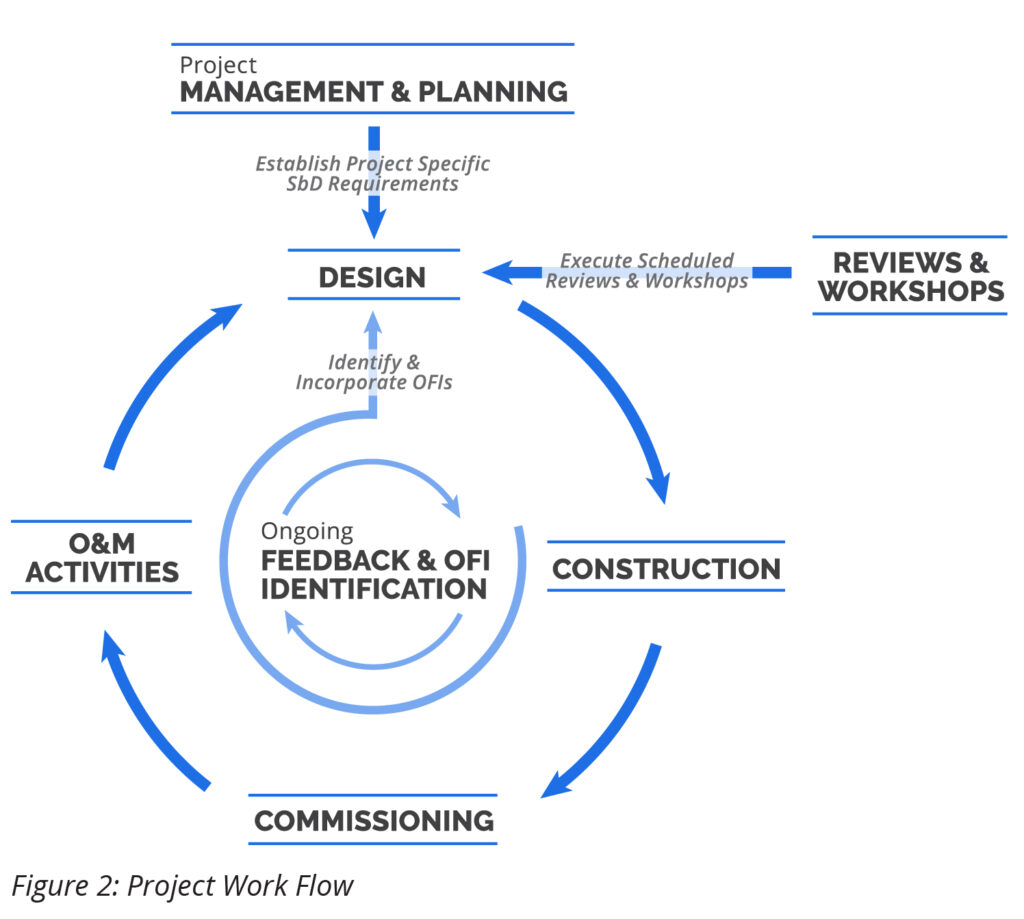
The practice is commonly called Prevention Through Design. It is the systematic assessment and mitigation of facility hazards that can arise during construction, operation, and maintenance.
There are several critical activities and tools that can help architects and their teams provide designs that will safeguard employee health and well-being. This is the foundation of SbD.
The best time to alter design components to eliminate potential hazards is early in the design cycle (Figure 3). The objective is to incorporate safety solutions during initial planning and design – when choices can best be controlled – for upcoming construction, operations and maintenance. There are two priorities at the start: design to reduce the risk of hazards before they happen and design so that hazards can be mitigated if an incident does occur.
As the design progresses to 35 percent and 65 percent completion, projects typically go through an Independent Technical Quality Control Review, or ITR, which involves a team of design experts looking for compliance and design improvements. This is the ideal time to ask reviewers to assess the project through a safety lens. These additional team members could be constructability, commissioning or building operations professionals, each reviewing a project from a different angle.
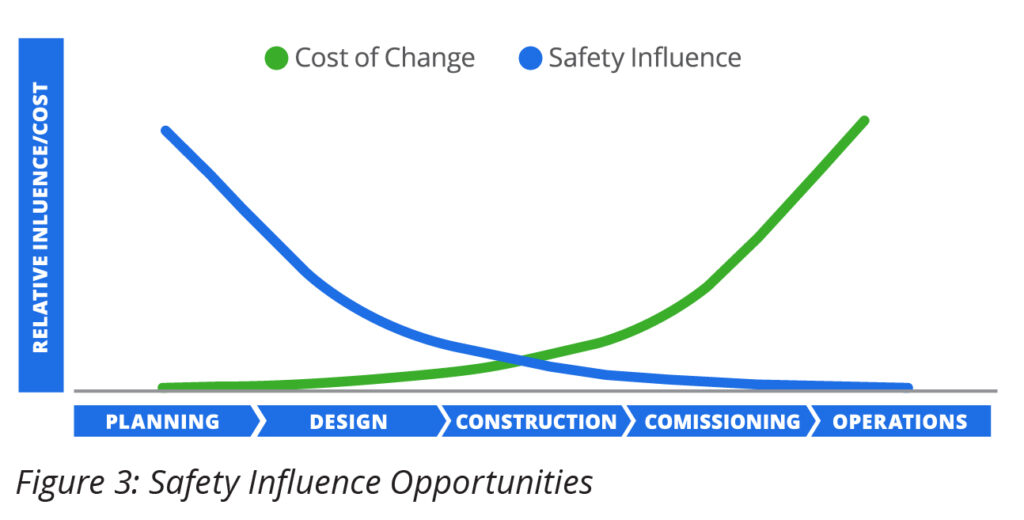
The SbD process starts with a workshop. Workshops are an excellent way to identify, understand and prioritize risks from the owner’s perspective and integrate specific safety and operability considerations.
A workshop is typically held after the preliminary design elements are defined. Comments then can be integrated into the detailed design, allowing impacts to the project schedule to be optimized. These workshops, which sometimes span multiple days for large facilities, can provide a systematic review of potential safety hazards. A later workshop can perform similar checks on more detailed design development. At this point, the object is to prevent significant changes and rework to the design. Checklists can help the team consider typical and project-specific SbD topics (Figure 4).
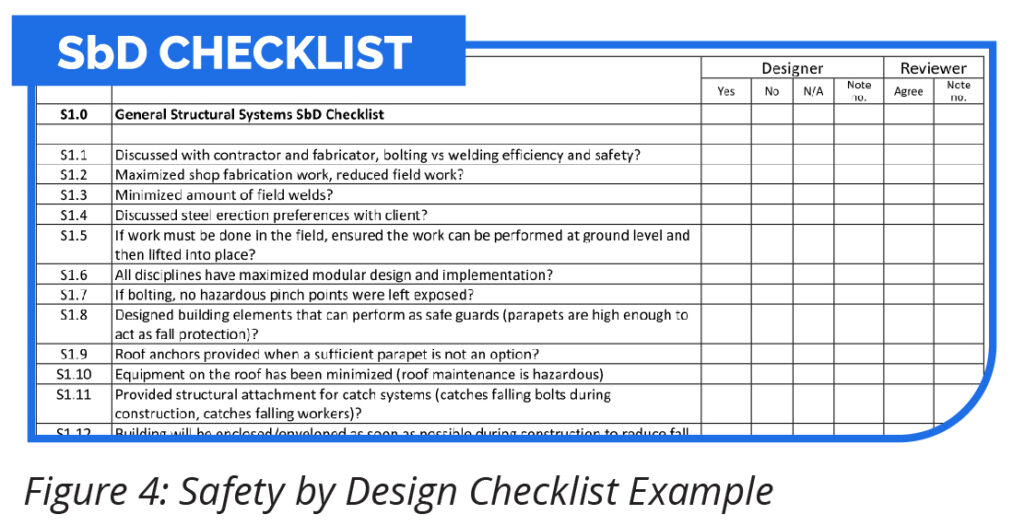
Safety design issues that architects should consider:
- Platforms to make operation and maintenance (O&M) safer.
- Reduce building components that require elevated work to install.
- Provide egress space for maintenance operations and a safer egress route.
- Dedicate space to safety equipment and systems.
- Encourage providing adequate program square footage to promote occupant safety.
- Consider the floor surfaces to reduce slips, trips, and falls in offices.
Teams can also employ technology such as Building Information Management (BIM) models and virtual reality.
A BIM model is typically used with SbD to provide a 3D virtual review platform. The BIM/3D model shows a project’s spatial aspects, including access, lifting, confined spaces, and other considerations. Piping and instrumentation diagrams (P&IDs) and other 2D deliverables, along with designer-furnished checklists, supplement the 3D model. The designer or third-party facilitator generates a SbD report that documents the findings, actions, and the ultimate resolution of all identified actions.
VR and augmented reality (AR) tools can make SbD workshops even more effective. These tools create a realistic walk-through of the facility, supplementing the more traditional 2D drawings and 3D model navigation review. An AR/VR walk-through provides a more intuitive platform than even a 3D model navigation software package because it’s easier to experience relative distances. The AR/VR model enables reviewers to stand next to equipment, piping, doors, and similar features, and see exactly what an operator or maintenance worker would. This virtual environment offers a better assessment of access points, interferences, removal restrictions, and other potential safety problems.
CASE STUDY: Safety by Design in Action – Designing a Safe Access
Many considerations go into ensuring safe construction, commissioning and operation. Among them is foot traffic.
Even though traffic volume would be low in this area, the team worked with the supplier to change the location of the door to the end of the building, decreasing the potential for a worker getting struck. Safety was improved without cost impacts.
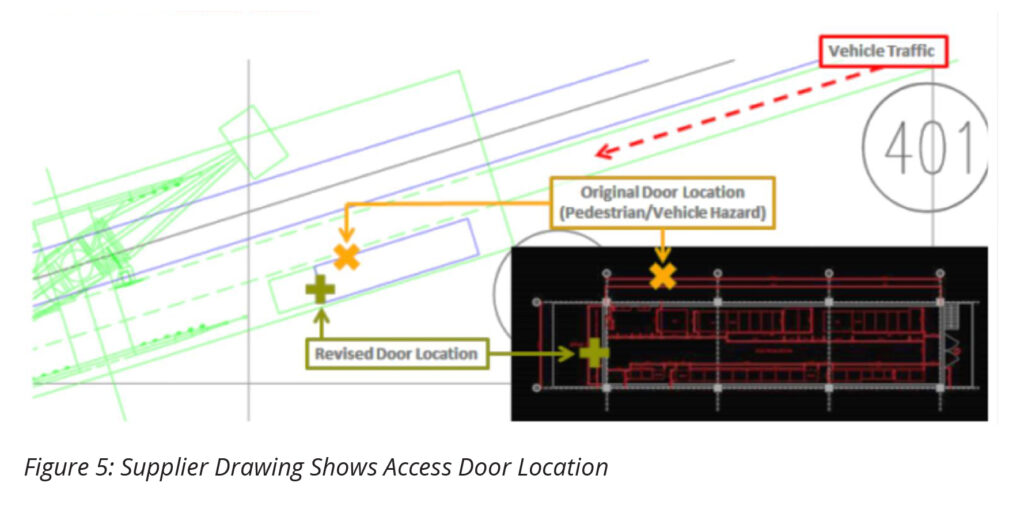
KEY POINTS:
Simple walkway design modifications can improve end user safety.
Design review meetings can identify SbD opportunities that can add long term value to the end user.
SbD provides multiple benefits to projects. First and most important, it helps protect the health and well-being of employees through the life of the project – starting with the first construction workers to the operations and maintenance staff who keep the facility functioning over its life. Improved safety also has a direct impact on monetary and social costs. Facilities designed with a focus on safety benefit while under construction, when they begin operations, suffer less down time and fewer lost work hours, and have a lower potential for corrective costs, including rework and legal costs. When properly implemented, the benefits extend to adjacent stakeholders through reductions in environmental and physical safety issues, helping to ensure that everyone can return home safely each day.